Breadcrumbs navigation
- Home page
- About Moser
- Blog
- AT THE GLASS WORKSHOP: FOLLOW THE BEAT AT THE HEART OF THE MOSER MANUFACTURE
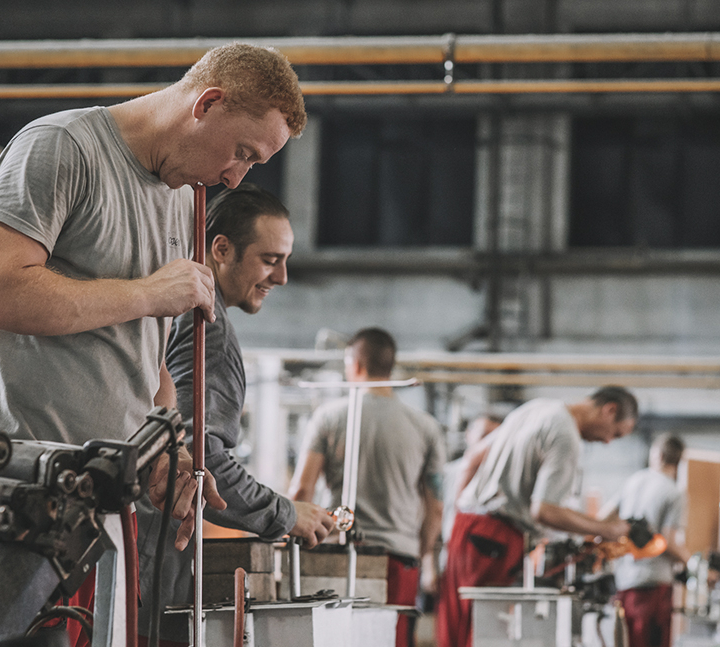
AT THE GLASS WORKSHOP: FOLLOW THE BEAT AT THE HEART OF THE MOSER MANUFACTURE
The place which pulses, or thrums more like, and where the temperature for an average human requires the aid of a towel.
After stopping at each of the manufacture’s individual preceding segments, we’re finally at the very spot – welcome at the werkstatt!
It’s right here, at the elevated wooden deck with three divided furnaces, where the crucial things are happening. Without the glass workshop, there would be no cutting or engraving production as there would be nothing for shaping or decorating. This is the place where glass begins to write its story, first time as an object made of a living liquid substance. Come with us, we’ll take you within reach of the furnace heat.
The batch makers were the first ones we visited. Therefore, we’ll skip a little and go directly to the night shift. The batch takes its time (at the temperature of 1340-1470 degrees Celsius) and so the melting, fining and the subsequent cooling / stabilisation to the working temperature 1150-1250 degrees Celsius has to be done at night, before 6.00 AM when the glassmaking teams arrive.
Each of the three furnaces has four openings where the same four-membered group meets every morning with clearly assigned tasks and roles. The lamp maker takes care of the molten glass, scrapes it and most importantly – with the help of a metal pipe, he takes the first dose from the furnace. One end of the pipe is isolated from the heat by special metals to ease the carrying and blowing, the other end is also made from metal material, in this case non-reactive with the molten glass. After the glass is born through the initial glass bulb, a whole range of glassmaking tools have their say in the process. For example, have you ever seen a glassmaking ladle – the wooden tool used for shaping the hot molten glass until its malleable, easing the subsequent blowing of the final shape as much as possible. Apart from a little bath with water for cooling the pipe, you can also find many others here: scissors of various sizes and shapes, tweezers, choppers and pliers…and, of course, we also can’t forget about so-called “little horns”, which the glassmaker uses for leaning the pipe and its gradual
rotation. Most glassmaking terminology has been historically adopted in Czech from German, that’s why they sound both foreign and familiar (for Czechs). The subsequent process then differs depending on the part of the day – if it’s morning or afternoon. Right at the beginning of the shift, the molten glass is the hottest, it has high viscosity, and therefore it’s the right time to work on smaller, drinking glass products (so-called cup production). Such pieces are made by the glassmaker’s assistant mainly. The master glassmaker then only comes to make the essential details, such as the bottom and the stem.
The time since morning flies fast and the atmosphere is lively both at and bellow the werkstatt. During breaks, and before they begin work in the precisely synchronised cycle, the glassmakers spend time in the so-called doctor’s office, that is a rest bench with drinks, non-alcoholic beer for refuelling ions included. As soon as noon approaches, it’s time for the bigger glass pieces, i.e. crystal objects (vases, bowls etc.). At this stage, the assistant starts his role as he helps the master glassmaker to manipulate the usually large and heavy mass. The blown glass can be either made “free-hand” or the master uses the pipe to blow into a form (which we have already talked about in our series “Craftsmanship up Close”). The form is made of wooden components precisely according to a pattern, connected with hinges and having several holes for draining steam (arising from the contact of hot molten glass and wood). To blow the molten glass into the form correctly is true mastership as the risk of not filling form grows increasingly with the cooling and decreasing viscosity. Therefore, the work has to be done extremely quickly, and also precisely and synchronised. The next steps differ with the type of the product.
With under and overlaid glass, the glassmakers apply layers in order to achieve colour effects, highlighting etc. Here, even more so, there is no time or space for hesitation, and the assistant has to be well coordinated with the master with the pipe and its handing over. Then, the inner tension / thermal stress of the hot glass has to be levelled to prevent breaking, and therefore nothing can be hurried. Next, the product is taken over by the carriers, who take it on a fork (the drinking glass) or on a cart with wheels (larger objects), to cooling furnaces, using the original pipe to put it in. Then, the machine ensures that the cooling process is gradual according to the set cooling curve. In the next stage, cold water is poured over the end of the pipe and, with the use of a chopper, it’s separated from the product. Here, the pipe’s cycle beginnings anew. For us, it is the end of the tour. Or at least regarding the glass workshop. Are you all sweaty? Well, you didn’t even have to lift the heavy molten glass at the end of the pipe. This job clearly can’t be done by just anyone, even the glassmakers themselves know it’s a tough job. Still, they all also add immediately that a more beautiful job doesn’t exist.