Breadcrumbs navigation
- Home page
- About Moser
- Mastery of hand-crafting
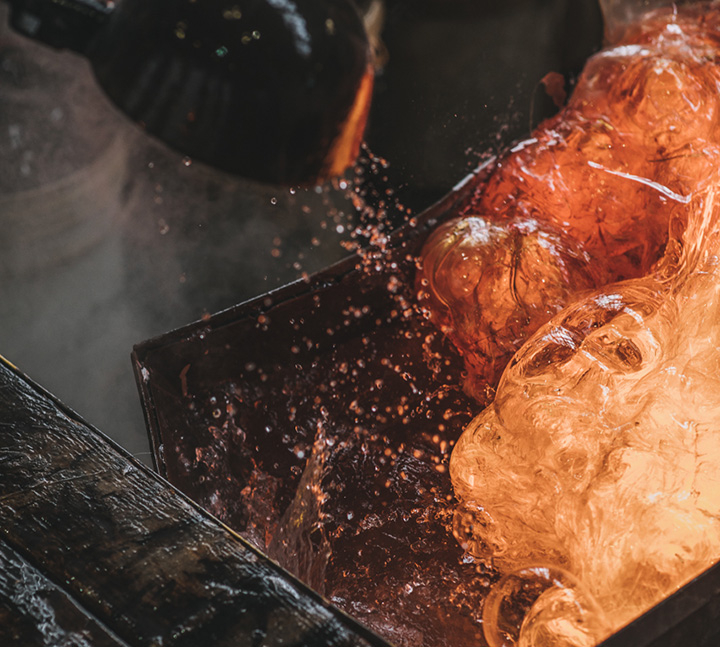
Mastery of hand-crafting
Ludwig Moser, the founder of our glassworks, was an inspirational person. A visionary, driven by his desire to push the boundaries of what it’s possible to create with lead-free crystal glass as far as he could. An artist who introduced exclusive décors and unique colours to the world of crystal glass. And, most importantly, a man who managed to gather together the best glassmasters to create things never seen before.
More than 167 years has passed but we are still faithful to his legacy. Every glass, ornament or art object goes through as many as forty pairs of hands before their beauty illuminates your abode. Let us take you on a journey from the first sketch to the final fine packaging.
It all begins with an idea
Prominent artists from all around the world contribute to Moser designs. There’s one thing they all have in common: they honour the unique nature of the Czech lead-free crystal and enrich it with their design vision. The clear beauty of our crystal artifacts begins with a clean sheet of paper. The designer sketches his idea and hands the paper over to the glassmasters. They, using their experience and practical tests, add technological directions, which then accompany the artwork through the whole production process.
Wood and metal in service of a glass
The blueprint is used to create a template, which is then handed over to “castmakers”. That’s when the wood comes into the picture. Our casts are usually cut and carved out of hard, fresh beechwood or pearwood. We even planted our own pear orchard to provide the best possible material for future generations of enthusiastic glassworkers. Sometimes, we use metal casts, especially for blown products or ornaments that are not round in shape. There is, however, one thing all the casts have in common: whether they are made of wood or metal, they have to be manufactured with absolute precision to fulfil the demands of the designer perfectly.
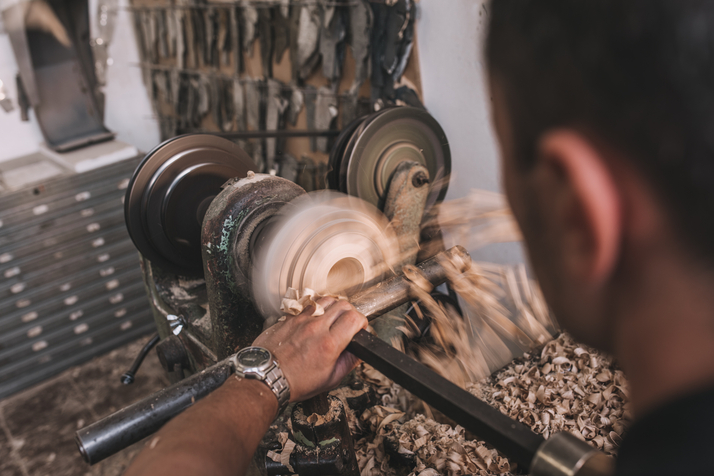
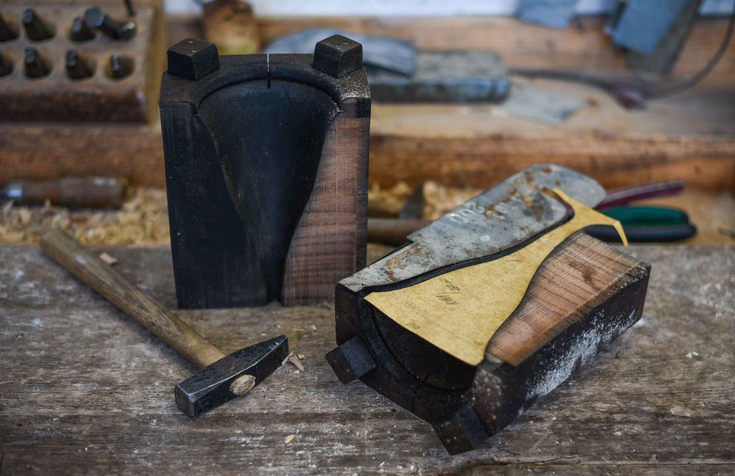
Lead-free crystal glass protects both health and the environment
Right now it’s time for glass. Shards and the glassworking batch (a mixture of glass-making sand, soda, potash, limestone and other ingredients) is melted at temperatures of around 1,500 °C. Then the furnace is left to gradually cool down. In the morning, at the beginning of the shift, we manufacture small pieces, as the material is at its most pliant. During the day, as the temperatures fall and the glass batch gets denser, it’s time for larger, more massive pieces.
Moser glass has very specific properties, especially as it doesn’t include any softening addition of lead. This confers several advantages at once. Lead-free glass is good both for environment and the health of the people working it. Its composition also makes it harder, so the most delicate patterns can be engraved into it, and it’s easy to colour or stain. Simply put, Moser’s ingredients give crystal glass the hardness of rock and the purity of lead-glass, all while not harming people or the environment.
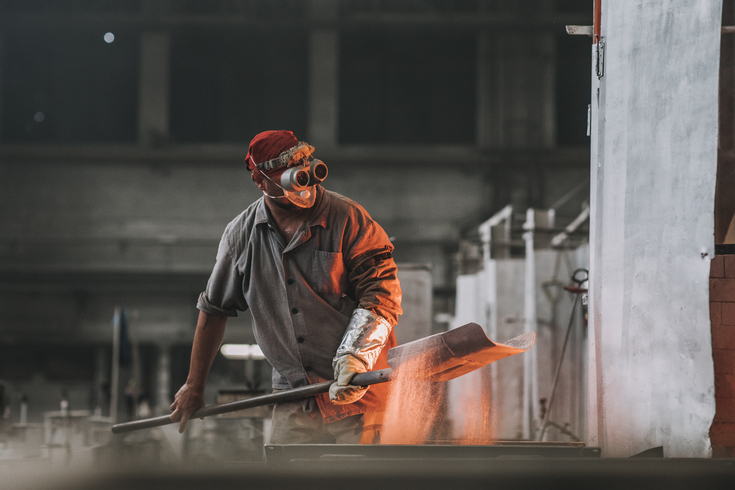
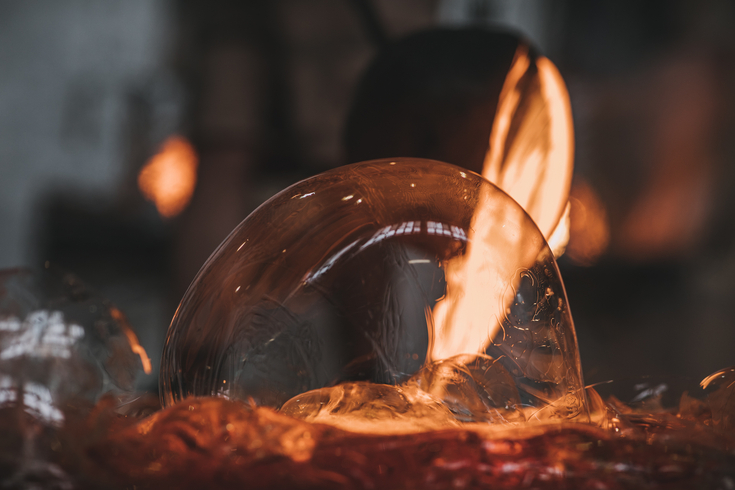
Unique Moser colours
Moser glassworks is world-renowned for its work with colours. The unique Moser colour palette is based on the colour hues of selected gemstones, like alexandrite (light violet), beryl (light green), topaz (honey brown), rosaline (light pink), aquamarine (light blue) and eldor (yellow). To acquire these unmistakable shades, the crystal is melted along with a selection of rare earths and metal oxides. The colours are very subtle and sophisticated, setting the Moser glassworks apart from their competition. Besides full-colour items, the Moser colours also appear in a flash variant, with a colour layer on the surface, and underlaid examples with a colour layer inside the crystal piece. These glass varieties use the colours amethyst (violet), reseda (green-yellow), pink, blue, aurora (orange) or green.
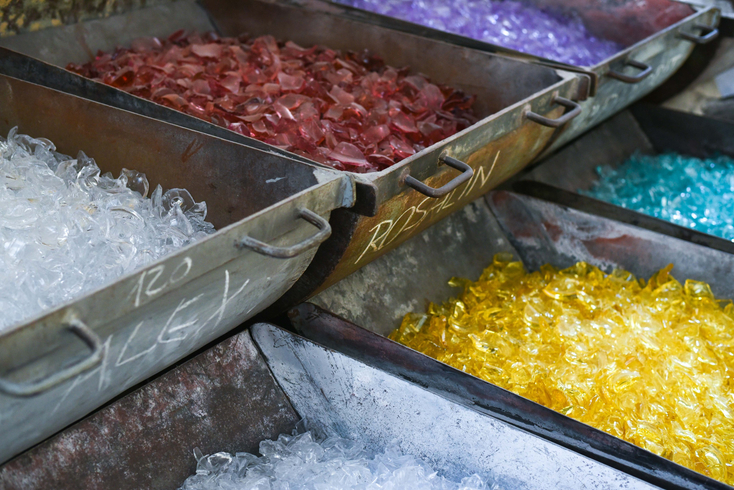
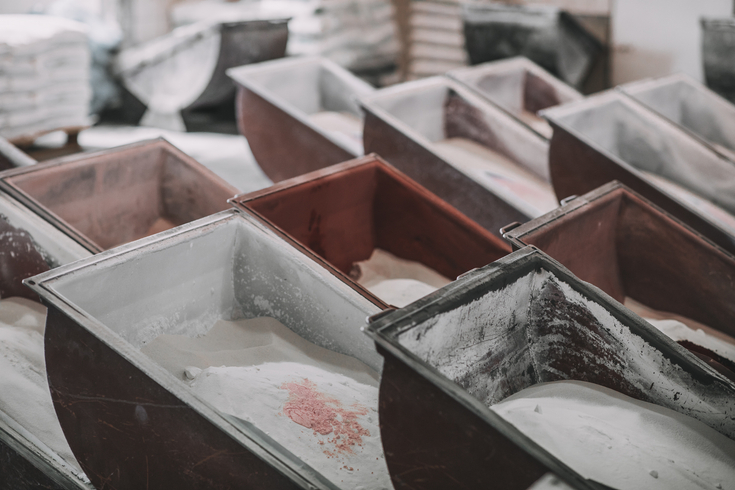
Moulding as a team effort
The magical, glowing substance, born in the fire, is moulded by the strong breath and skilful hands of experienced glassmasters. Blowing glass is a team creative process: the gatherer, the boy and the gaffer work together to give the drop of melted glass its desired shape.
The gatherer gathers the material to a blowpipe. The boy adds more glass and using his breath and various tools pre-moulds the future jewel of the glassworking craft. Only now is it time to blow into the cast that will give it its proper shape and size.
The glassmaster is in charge of the final steps. He expertly wields metal and wooden tools and instruments and, if necessary, heats the emergent article in the furnace. To make sure the result is perfect, he checks the proportions and size using a metal template. Only when he’s absolutely satisfied with the product, the carry-in-boy takes it to the annealing furnace. There, the glass, depending on the thickness of its walls, cools down for a period of a couple of hours to several days, before heading to a thorough quality control. The smallest imperfection means that the product returns back to the furnace as shards.
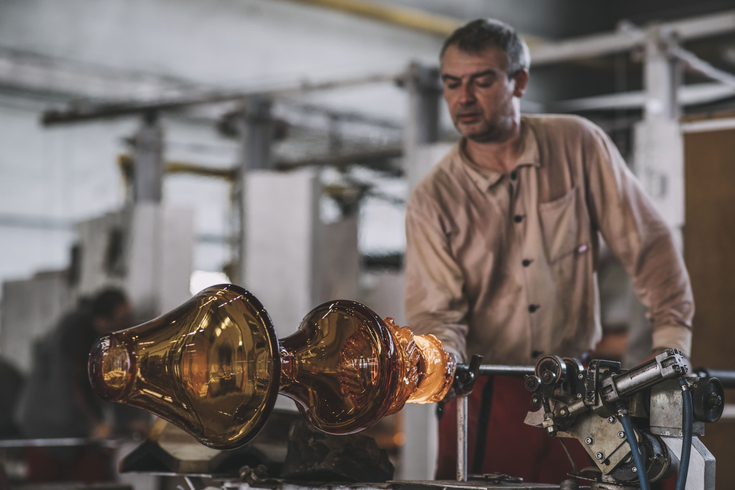
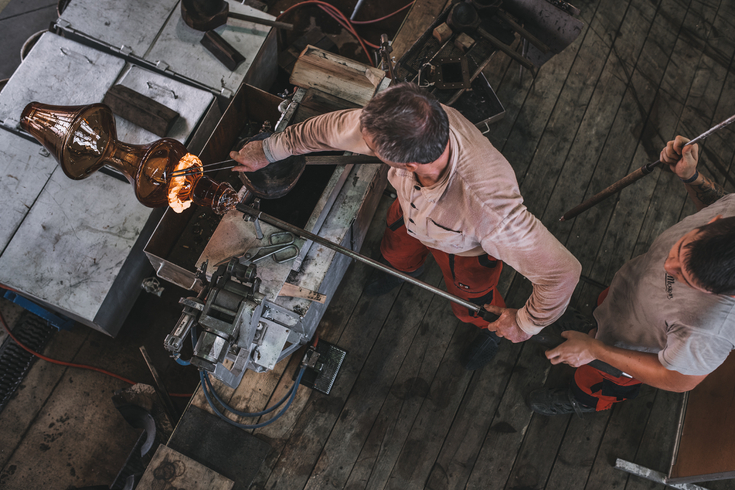
First products done. As long as they make it through quality control
Time for delicate handywork. The products are neatened precisely in order for their shape and the purity of the lead-free Czech crystal to stand out. It’s only if the second quality control considers them to be uncompromisingly flawless that they can be cut and decorated further. Smooth products with no décor can be shipped to customers at this point.
Mastery of the decorative cut
The fate of every piece is now decided by the cutters. You’d recognize them easily. Clad in aprons, with plugs in their ears and hearing protection, sitting on tall chairs from which they can maintain total control over the cutting.
The facet cut is done on the surface of a horizontal grinding wheel, which makes it flat. The rounded cut is done on the perimeter of a vertical grinding wheel, creating a curved surface. It all begins with an initial cutting stage with rough grains known as carbo, which removes the unnecessary glass mass. Then it’s time for cutting and smoothing, when the product receives its final shape, and then several stages of final polishing to a high gloss. The end result is a piece of a size and shape perfectly in-line with the artist’s vision and a surface close to perfection.
After cutting, there’s another quality control. That decides whether the product can be handed over for further decorating or, if it’s finished, for packing and shipping.
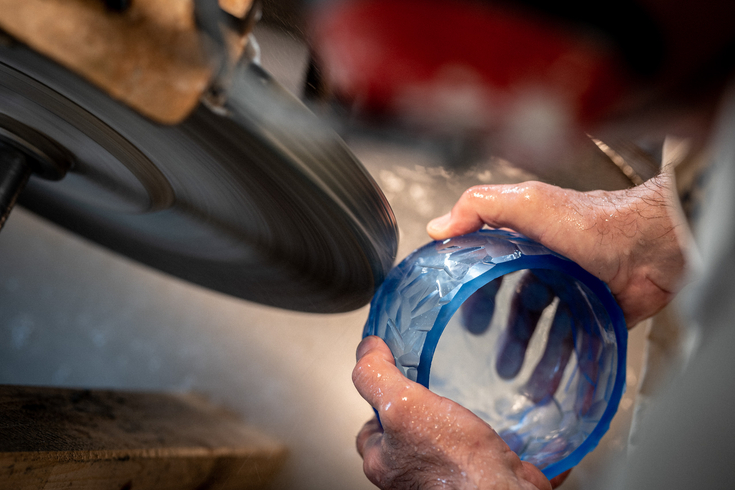
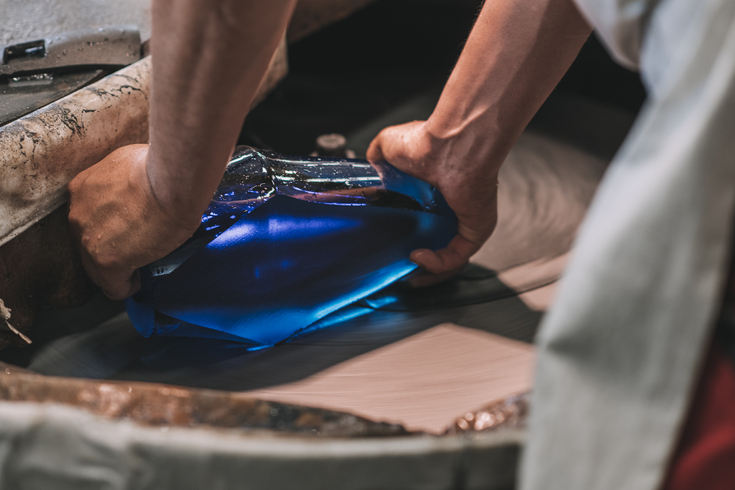
Decoration with precious metals
Painting glass has been numbered among Moser’s crowning techniques since the glassworks’ founding. The most exceptional is, of course, plating with 24-carat gold or platinum. Before decorating, every piece of glass needs to be painstakingly cleaned. Only then will the painters place the templates and apply the metallic solution on the crystal. The result is a perfect glass edge, or complicated patterns and décors, as defined in the technical specifications. Depending on the type of metal, one or two layers are created. After being fired in a furnace, the matte gold décor is hand-polished with agate and hematite.
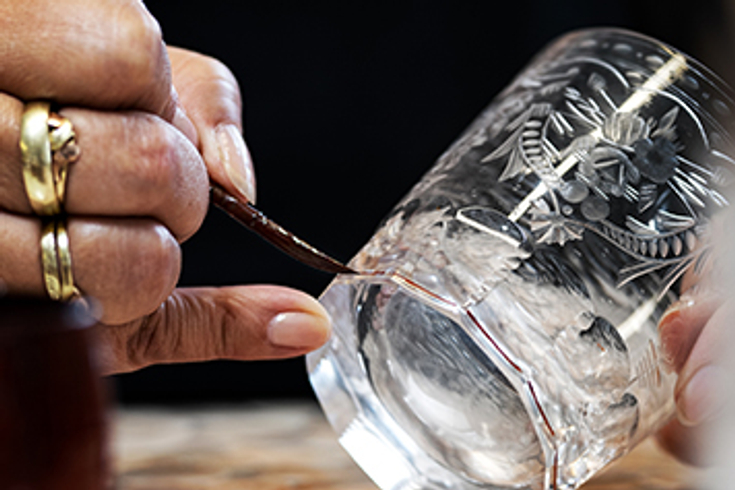
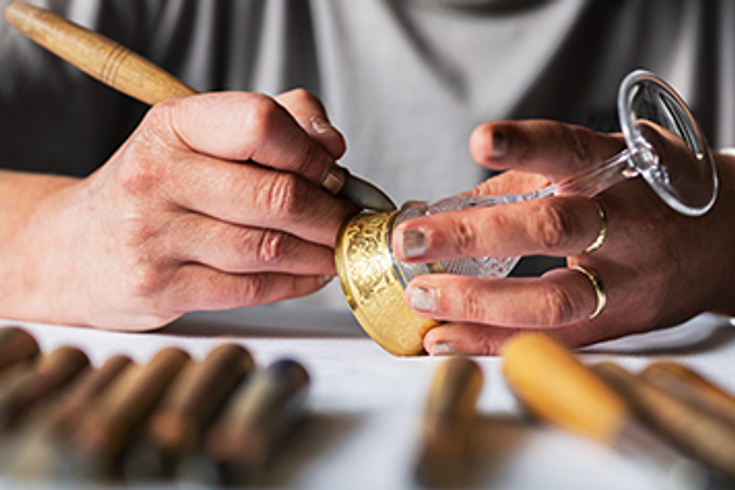
Engraving that takes weeks and months to make lasts forever
The most graceful and sophisticated decorating technique, developed by Ludwig Moser and his followers to a previously unseen level, is engraving. Its perfect execution demands an experienced artist. It requires remarkable talent, aesthetic feel, strength, craftsmanship and extraordinarily meticulous precision. Those are the talents of the elite engravers of Moser. One of them, Tomáš Lesser, received the knighthood of the Order of Arts and Letters in France in 2020.
The required motif is first drawn onto a thin paper and then transferred onto the vase or other glass piece. To make the spot for the engraving easy to see, it’s marked with chalk and water-resistant marker. Only then does the engraving itself start, with the engraving master removing the crystal using grinding paste and small wheels fitted to the engraving machine. One engraving can take its author weeks or even months. Time is not of the essence here: it’s the result and its perfection that counts.
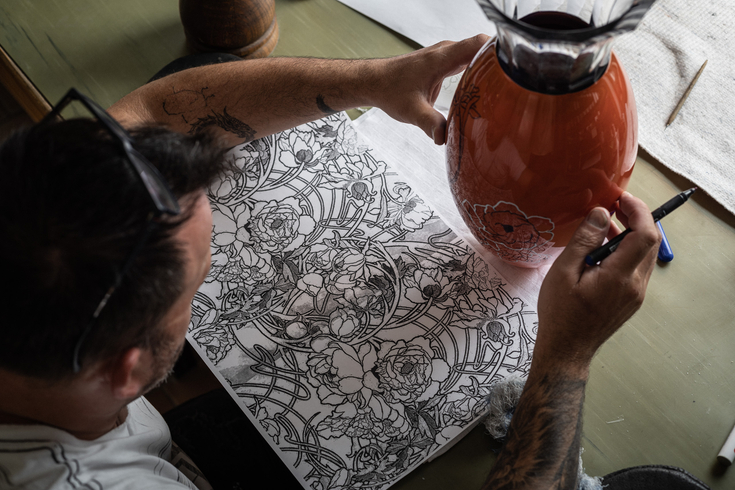
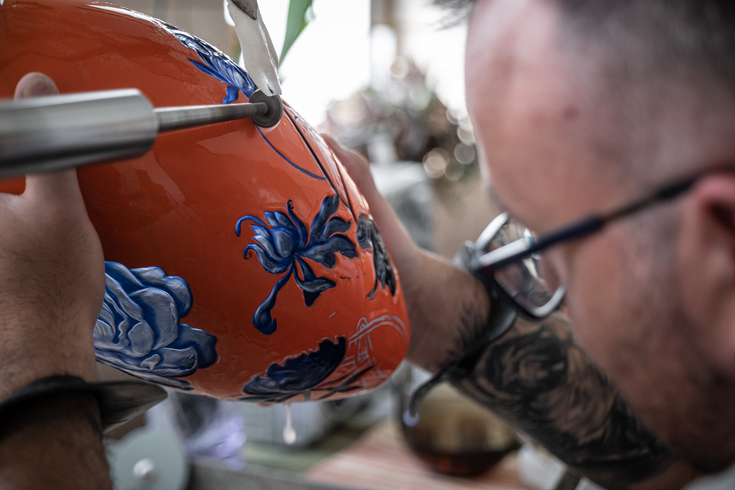
Last step on its way to you
All finished products go to the centre for final quality control. Only those that comply with the most stringent quality requirements are then marked with our logo. We also issue a certificate which confirms the origin of the product in our glassworks, and a card with the numeric code for the quality controller, whose uncompromising oversight has confirmed the quality of the product.
Exclusive products deserve an exclusive package. We put great effort into the appearance of our packaging, but we care for the environment as well. That’s why most of the materials we use are fully recycled. We are proud of the fact that, thanks to our well thought-out process, 99.85% of all shipped packages reach our customers in perfect condition. We look forward to you becoming one of them.