Breadcrumbs navigation
- Home page
- About Moser
- Blog
- I learned from the greatest masters, says glassworker Zdeněk Drobný
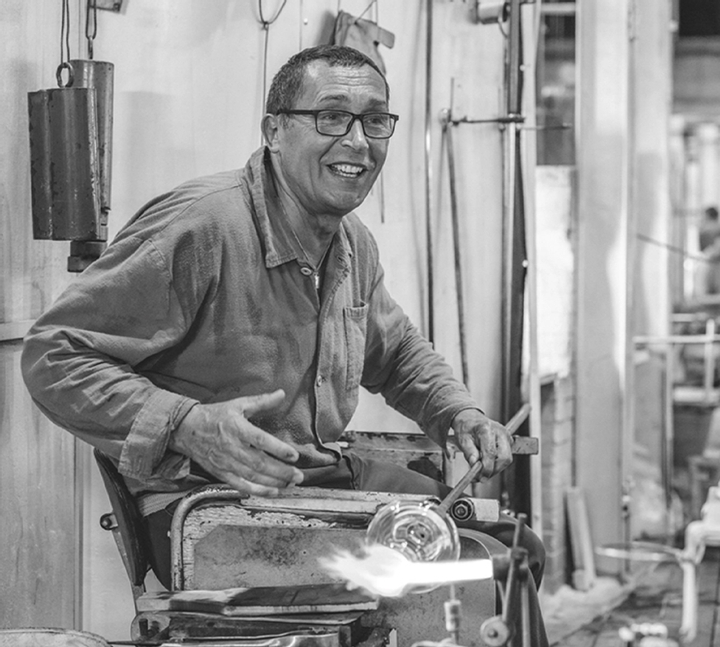
I learned from the greatest masters, says glassworker Zdeněk Drobný
When he was young, he used to play with shards of glass from the dump; now he ranks among one of the best glassblowers at Moser. Not that he would never say so about himself. “Every new form requires patience and careful testing,” says Zdeněk Drobný, explaining why his craft has never ceased to fascinate him and why his interest in glassblowing will continue even after his retirement.
Your parents also worked at Moser. Is that why you got involved in glassblowing?
Yes. Our family lived a hundred meters from the glassworks in one of the apartments intended for the employees at the time. My mother was the one who mostly worked at Moser at the time, and so I often went to play under the windows of the glassworks. I also used to go there to watch the glassmakers at work in the plant and it fascinated me how the masters worked with the glass and changed its shape. Glassblowing was pretty much a given for me.
Who influenced you the most at the beginning?
Mr. Antonín Motl, our training master at the time, taught me my first steps. But in my third year the master Mr. Schmiedkunz took me under his wing, perhaps he saw some potential in me. Thanks to him I completed the rest of my training in his group as a bellowsman.
That’s some good motivation for a young person.
Yes, but that wasn't all. Mr. Schmiedkunz was a very well educated, skilled, and fair person, a true master of his craft. He taught me a lot and gave me a lot. He could tell I was very interested in glass, and so he stayed with me at the glassworks after business hours every Friday. He spent two and a half extra hours there with me every week and taught me everything I wanted or needed to learn.
How was Mr. Schmiedkunz different from other masters?
In his precision and discipline. I will never forget how I was once chatting with a colleague at work. He came to me and explained that we can't do two things at one – either we were all going to talk and we’re not going to work, or we were all going to work, and that meant we couldn’t talk. I realized he was right. For our craft it is enough that you look away for a moment, and you can already ruin the product. When I broke a glass bowl, for example, by not paying attention, I had to spend more time at work, without taking a break, because they paid us for the number of pieces we made. Mr. Schmiedkunz taught me to concentrate fully on my work.
What was the hardest part of the production for you?
Overcoming my fear of the heat and getting used to it. In the beginning it took a while, everyone needs to gradually learn all the steps in order to advance. The first two weeks we learned with the jacks, we had to master the exact fingering, just like musicians learn how to play the piano. The goal was to master the fingering so much that the jacks turned fluidly and didn't wobble. And we weren't even working the furnace yet! Then we learned to roll the rollers, and only after that did we learn how to gather molten glass onto the blowpipe. At the same time, every training master held our hands so we wouldn't jerk away, even if it burned us. That kind of heat bothers a lot of people, but I’ve been happy to see that there are a number of young and talented folks at Moser who are willing to stand it.
You say it takes a long time before a person adopts the whole process of creating glass objects enough to do it properly. When did it first occur to you that you were starting to get good at it?
I’m still not good at it even now. I’m still learning. One big challenge for me was when Lukáš Jabůrek became the creative director of Moser. He designed glass vases in shapes and sizes I had never done before. And so I had to begin slowly, step by step, first with smaller items. Gradually I worked my way up to the bigger ones, like the Pear vase, which we had to buy new blowpipes for, 26 millimeters in diameter. The color was a challenge for me as well. But of course I am glad, I liked that Lukáš Jabůrek introduced some new items among the existing Moser products. It was interesting for me to meet with other artists like Jiří Šuhájek, Oldřich Lípa, or Vladimír Jelínek, who approach glass completely differently. And in my spare time at home when I draw diagrams and think about them, I imagine them the way the old masters would make them.
Aren't you a little hard on yourself?
You know, we glassblowers don’t like to give praise. Instead we’re more likely to criticize people, because we believe that too much praise leads to a certain stagnation. But of course it is necessary to acknowledge people and motivate them.
You mentioned that you meet a lot of young talent in the glassworks. What does that mean to you?
I think it’s great that there are several young people at the glassworks who are clever. Just now I noticed one apprentice who arranged an internship over summer vacation and comes here regularly to blow glass. He can already handle the basics beautifully. It also really motivated me back before weekend shifts were introduced when I stayed in the workshop voluntarily with a couple of guys and we tried out different kinds of old techniques, such as glass sticking. My son helped create the form and thanks to a team effort we pulled it off.
In 65 years you are still able to blow the largest forms. You must have immense lung capacity.
Yes, that’s why I do a lot of sports. You have to when you do physically demanding work. I ride the bike a lot, also with folks from Moser! Sometimes we are even joined by the director of the company, Pavel Mencl, or the owners the Zapletals. I’ve never experienced that such high-ranking people would hang out with ordinary workers. I like that about Moser.
And yet you are planning to retire next year.
Yes, I figured I should quit while I’m ahead. I’m the competitive type and I always want to keep pace with the younger generation through my work. But when you see that younger glassblowers are becoming better than you, then it’s time to make room for someone who needs to grow. That's why I agreed with the head of the plant that I will end my employment with Moser in June of next year. But I don't rule out coming to help if someone gets sick and they need to find a substitute. Moser gave me a lot and I am happy to give back.
Do you also have Moser works at home?
I can only drink from Moser glasses! Ever since I was born I've been drinking water only from Moser glasses. It would never even occur to me to use a different glass, good water would go bitter in my mouth. And as far as vases go, I have one – it is truly unique, and I made it myself. It has an oval shape, blue on one side and green on the other. It's essentially two vases in one. It is the only piece of its kind in the world.
Zdeněk Drobný
He first came to Moser for an internship in 1971 and now celebrates 50 years working here. He began coming to the glassworks when he was fifteen years old. He is the only one who can blow the large model of the Pear vase; the blowpipe gathers 30 kilograms of lead-free crystal in making it. In his opinion, the work of a glassblower must always be quick and precise.