Breadcrumbs navigation
- Home page
- About Moser
- Blog
- Maharani. How is one of the best-selling sets born?
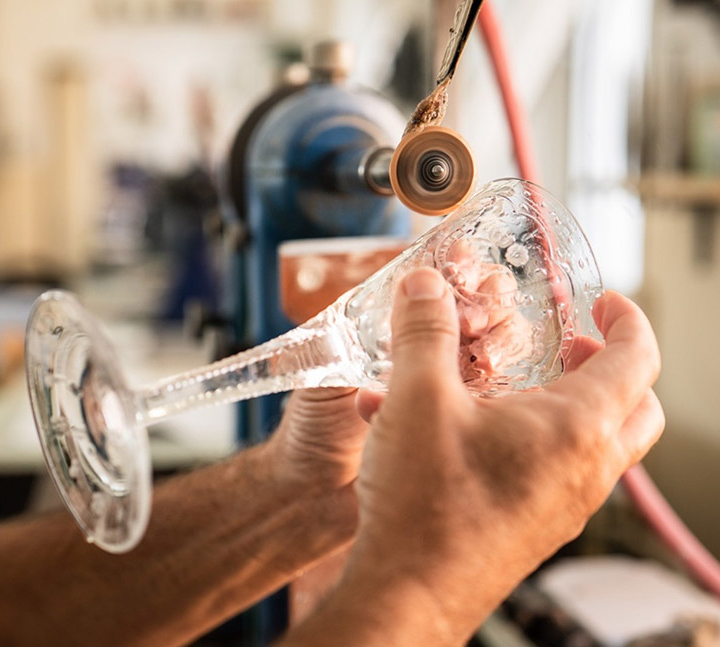
Maharani. How is one of the best-selling sets born?
A collection which blooms under the hands of glassworkers, cutters, and, most significantly, engravers and painters. Later on, this set, strewn with delicate flowers, will be held by people enjoying their favourite drink. The Maharani collection of drinking glassware and decorative items, crafted with particularly complex techniques, is one Moser's best-selling sets. Its delicate curves and floral motifs created with utmost precision have been a hit worldwide since the year 1895. How long is the journey which these crystal masterpieces must travel in the glassworks before they arrive to your festive table?
The manufacturing process involves the work of approximately 30 professionals. What are their respective responsibilities?
- Preparation of the glass batch, 2 people
- Melting, 2 people
- Preparation of the wooden mould, 1 person
- Blowing the product, 4 people
- Quality inspection (following the cooling of the product), 1 person
- Cracking-off, where any unwanted parts are removed off of the cooled product, 1 person
- Grinding the rim, the foot and the stem of the product smooth, 5 people
- Rinse after initial grinding, 1 person
- Quality inspection 2 (following initial grinding), 1 person
- Marking out for decorative cutting, 1 person
- Decorative cutting with a disk grinder, 4 people
- Inspection following the decorative cutting, possible corrections, 2 people
- Engraving, inspection of the engraving, 2 people
- Glass painting, gold polishing, glass firing, 2 people
- Final quality inspection, signing, packaging, certificates, 2 people
What are the main steps of the manufacturing process? Blowing, grinding, engraving, painting. Let's take a closer look at them.
Melters and glassworkers
The journey of the Maharani collection begins in a glass furnace, where each item is blown into moulds. In the initial phase – in the glassworks, the manufacturing process is identical to that of other sets. The true adventure begins in the glass shops.
Cutters and edge-cutters
Maharani features a traditional cut, which is used in almost every drinking glassware set. However, the edges are decorated with small beads, which are, in fact, minuscule cuts. "People often believe that the beads are only created in the engraving shop, since they are so tiny. This is actually the cutters' job, though," explains Martin Prokeš, the glass shop's technologist.
Engravers
They catch your eye right away – delicate classical bouquets, which adorn the Maharani collection products all around the perimeter (the so-called mantle). These are the work of engravers, who proceed carefully, millimetre by millimetre, and engrave individual motifs into the glass with unmatched precision. Another notable feature is the rim made of the so-called olive beads, which require regular polishing. "It is extremely rare for a collection to include so many different techniques and approaches," says Martin Prokeš.
Before the engraver gets to work, the motif must be marked out on tracing paper. The sheet of paper is subsequently inserted, for example, inside the body of a glass. The engraver traces the decorum with a permanent marker, which will not wash away with water, and engraves the decorum step by step. The engraving is always based on the original historic patterns, which are safely stored inside the Moser archives. "We guard the originals carefully, so we are able to come back to them anytime to ensure that there no deviation from them has occured," relates Martin Prokeš. Each engraver has their own method and combines different engraving techniques in various ways. You could say that each of them has their own handwriting. They are even able to tell the glass which they have engraved apart from other glasses. Only the engraver is able to identify their own work; to the customer, the nuances are indistinguishable.
Photography: David Švehla
A very distinctive engraving can be found on the jars. "It is no simple task, the jar is quite large and the lines must be traced with utmost accuracy, so that they are perfectly parallel to each other. We focus on every tenth of a millimetre," says Vlastimil Selinger, the local master engraver, who has been working at the Karlovy Vary based glassworks for over 40 years, and spent his first decade there engraving the Maharani set almost on a daily basis. "When it came to glasses, I usually managed to complete one piece per hour. Oh, the effort and time that went into the training before I reached this level of speed and confidence in my work! A skill is only obtained through years and years of practice, and innate talent," he reminisces with enthusiasm. "I have gradually moved on from collections to master level engraving and working on custom pieces, but when I occasionally returned to the Maharani collection later on, the engraving took me significantly longer. The muscle memory has simply faded away."
In fact, when new engravers are undergoing the initial training, they work on the Maharani collection, as it allows them to try their hand at all types of cuts and methods. "Intaglio cuts, half cuts, lines, beads, pulled cuts, polishing…" Vlastimil Selinger names a few. "You can learn the majority of what you need to know as an engraver by working on this set."
Painters
As soon as the engraving is finished, it is time for the brush and the precise strokes of painters to come into play. Hand painting a fine line on the stem of a glass is a particular challenge. "When it comes to other collections, the painter uses the engraving as a lead and they often paint right into it. Or, they may use a turntable – the glass then spins around and the painter holds the brush to it. But in the case of the stems in the Maharani collection, no such thing is possible and the painter can only rely on their own hands. There is no marking out, they just paint straight away. The precision and expertise are truly fascinating to me," relates technologist Martin Prokeš.
And why is Maharani among the best-selling collections? "It is rich, but not over-embellished. Subtle, but not lacking in any way. It is simply a well-balanced set, which fits into the contemporary style and is suitable for a wide range of interiors," Martin Prokeš reckons and Vlastimil Selinger adds: "Nowadays, I do not engrave the Maharani set anymore, however, I would love to come back to it. It has always been one of my favourites. I might ask my colleagues at the shop to let me do it again, just for a bit!"
Maharani in brief
It is one of the most complex sets, hand-engraving the floral motifs and hand-painting the fine gold lines being the most challenging techniques involved.
The collection was created in the year 1895, when it began being manufactured by the Meyr's Neffe Glassworks in Adolfov by Vimperk. The glassworks merged with Moser in 1922 and the collection has thus entered Moser's portfolio.
It only received its name in the 1920s, when the glassworks manufactured this set for Maharani Sethu Lakshmi. She was the regent of the Kingdom of Travancore in southern India between the years 1924–1931. The list of the set’s notable admirers also includes Mohammed V., the sultan of Morocco, Asfa Wossem, the Ethiopian prince, Sukarno, the Indonesian president, the royal family of Bahrain, or the Maharaja of Alirajpur.
It is one of Moser's best-selling collections.