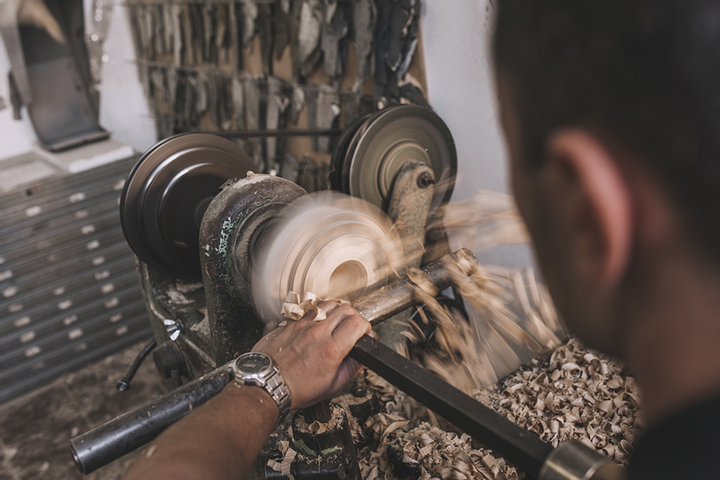
2020/09/22
Breadcrumbs navigation
We’re back! Returning with our tour of the glassworks, bringing the unique work of the artisans closer in Karlsbad, Dvory. This time, we head once again to the cutting workshop.
However, It’s time for the second, decorative grinding phase of this process. Therefore, we’re going to introduce some new glassmaking professions – cutters of facets and rounded shapes. Come with us, we’ll introduce you to this indispensable part of Moser mastership…
Just to make things clear, this is the place where the product arrives after its first cutting, with remains of the blowing removed, for example, when the grinded stems and bottoms have been added. Still, we speak about a semi-finished piece. However, with decorative cutting, the finishing line begins to draw closer. Stark definitions are sometimes for the good, therefore, we also specify that: “Decorative cutting covers grinding of both matt and polished cuts and facets.” Nevertheless, we are, by all means, speaking about a discipline that is, especially in Moser’s case, quite complex. So, let’s get an idea of the main techniques in the first place.
The best-known and typical type is definitely the facet cutting, used for decorating drinking sets, such as Lady Hamilton, Pope, or with a wide range of interior objects. The finest of all the cuts, so-called chequered cut, can be seen on iconic sets, such as Splendid or Royal. Finally, for grinding the product to a greater extent, we use a surface cut, as in the case of Iris or the Four Seasons vases collection.
What exactly do the facet cutters, do and what is the role of the rounded shapes cutters then? Both techniques share the same starting point: drawing the cutting sketch. This is to make sure that the cuts are symmetrical, to determine the pattern’s height, and also to give an idea about the distribution of individual types of the cuts. Vertical division is done by dividing machine, drawing lines on the product using a drafting pen with white enamel. White enamel is used as it isn’t washable once dry. For horizontal division, a semi-heavyweight machine with wooden discs is used. It imprints black indelible asphalt imported from Syria on the glass piece in horizontal circles.
One of the main differences then rests in the discs. Facet cutter uses the free cutting method on a horizontally placed disc, with 100% requirement for its straight surface. In this case the material isn’t removed by the disc itself, but by an abrasive material being brought on it by water. Abrasives are then scaled according to their graininess. The first cutting machine is equipped with corundum (mixture of silicon carbide), the second with softer corundum, and the last one works with a so-called micro-grain.
Rounded-shape cutters by contrast, have vertically fixed discs that are, unlike the facet ones, made of abrasives as such. The cutting discs go into the hard crystal and create convex or concave shapes. Rounded shapes cutters also proceed from the coarse-grained corundum to the finer. However, instead of micro-grain, they use melted aluminium oxide. After three grinding phases, two-part polishing takes turn with both techniques. For the first polishing, pumice (a material of volcanic origin known by anyone using nail files) is used. The finest polishing material is cerium oxide, which brings Moser glass with all of its acclaimed facets to the highest shine level – it adds flair and sparkle.
Apart from graininess, the rounded shape cutting discs also differ in perimeter and profile, i.e. in the shape of the edge. Small perimeter makes deep cuts, whereas big one is for shallow cuts. Rounded shape cutters then have a variety of shapes including rounded, wedge-shaped or skew ones. As already mentioned, the facet discs are much less complex in this sense – they just need to be strictly straight.
What are the other typical attributes of this place then? Earplugs or headphones and an apron, that is the mandatory equipment in the decorative cutting workshop. However, above all, strict cleanness is the governing principle. Every grain falling on a soft disc means a risk of scratching and the previous phase must be repeated. Therefore, after each cutting phase, the product has to be thoroughly washed, and only then it can be taken over by another cutter. In the event that the product is handled by the one who worked on it, both the cutter and his apron have to be cleaned.
What else then? Now, there is “only” another strict technical control left. Products with fixable defects go back, the flawless ones are sent for other types of decorations (gilding, engraving or sanding), or they’re handed over to the final control and sorting. Therefore, before Moser crystal goes from hand to hand to our customer eventually, there are still some stops to be made. Stay tuned and get to know Moser #CraftsmanshipUpClose fully.